Large industrial buildings, auditoriums, gymnasiums, theatres, hangars, and exposition buildings require much greater clear distance between supports than can be supplied by beam and column framing. When the clear distance is greater than can be spanned with rolled beams, several alternatives are available. These may be classified as girders, simple trusses, arches, rigid frames, cantilever-suspension spans, and various types of space frames, such as folded plates, curvilinear grids, thin-shell domes, two-way trusses, and cable networks.
Girders are the usual choice where depths are limited, as over large unobstructed areas in the lower floors of tall buildings, where column loads from floors above must be carried across the clear area. Sometimes, when greater strength is required than is available in rolled beams, cover plates are added to the flanges (Fig. 7.10a) to provide the additional strength.
When depths exceed the limit for rolled beams, i.e., for spans exceeding about 67 ft (based on the assumption of a depth-span ratio of 1:22 with 36-in-deep Ws), the girder must be built up from plates and shapes. Welded girders are used instead of the old-type conventional riveted girds (Fig. 7.10b), composed of web plate, angles, and cover plates.
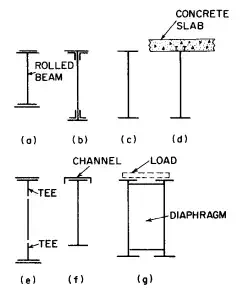
FIGURE 7.10 Typical built-up girders
Welded girders generally are composed of three plates (Fig. 7.10c). This type offers the most opportunity for simple fabrication, efficient use of material, and least weight. Top and bottom flange plates may be of different size (Fig. 7.10d), an arrangement advantageous in composite construction, which integrates a concrete floor slab with the girder flange, to function together.
Heavy girders may use cover-plated tee sections (Fig. 7.10e). Where lateral loads are a factor, as in the case of girders supporting cranes, a channel may be fastened to the top flange (Fig. 7.10ƒ). In exceptionally heavy construction, it is not unusual to use a pair of girders diaphragmed together to share the load (Fig. 7.10g).
The availability of high-strength, weldable steels resulted in development of hybrid girders. For example, a high strength steel, say A572 Grade 50, whose yield stress is 50 ksi, may be used in a girder for the most highly stressed flanges, and the lower-priced A36 steel, whose yield stress is 36 ksi, may be used for lightly stressed flanges and web plate and detail material. The AISC specification for allowable-stress design requires that the top and bottom flanges at any cross section have the same cross-sectional area, and that the steel in these flanges be of the same grade. The allowable bending stress may be slightly less than that for conventional homogeneous girders of the high strength steel, to compensate for possible overstress in the web at the junction with the flanges. Hybrid girders are efficient and economical for heavy loading and long spans and, consequently, are frequently employed in bridgework.
Trusses. When depth limits permit, a more economical way of spanning long distances is with trusses, for both floor and roof construction. Because of their greater depth, trusses usually provide greater stiffness against deflection when compared pound for pound with the corresponding rolled beam or plate girder that otherwise would be required. Six general types of trusses frequently used in building frames are shown in Fig. 7.11 together with modifications that can be made to suit particular conditions.
Trusses in Fig. 7.11a to d and k may be used as the principal supporting members in floor and roof framing. Types e to j serve a similar function in the framing of symmetrical roofs having a pronounced pitch. As shown, types a to d have a top chord that is not quite parallel to the bottom chord. Such an arrangement is used to provide for drainage of flat roofs. Most of the connections of the roof beams (purlins), which these trusses support, can be identical, which would not be the case if the top chord were dead level and the elevation of the purlins varied. When used in floors, truss types a to d have parallel chords.
Properly proportioned, bow string trusses (Fig. 7.11j) have the unique characteristic that the stress in their web members is relatively small. The top chord, which usually is formed in the arc of a circle, is stressed in compression, and the bottom chord is stressed in tension. In spite of the relatively expensive operation
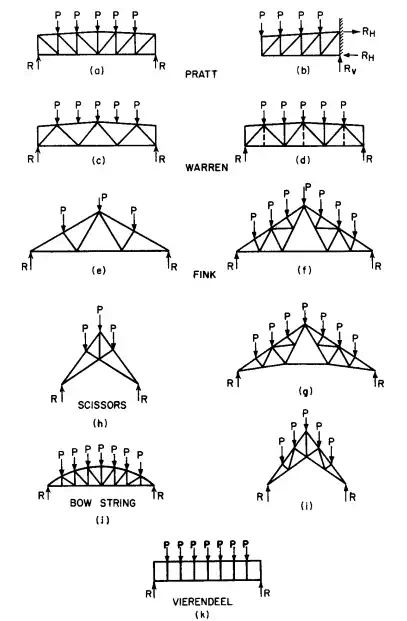
FIGURE 7.11 Types of steel trusses.
of forming the top chord, this type of truss has proved very popular in roof framing on spans of moderate lengths up to about 100 ft.
The Vierendeel truss (Fig. 7.11k) generally is shop welded to the extent possible to develop full rigidity of connections between the verticals and chords. It is useful where absence of diagonals is desirable to permit passage between the verticals.
Trusses also may be used for long spans, as three-dimensional trusses (space frames) or as grids. In two-way girds, one set of parallel lines of trusses is intersected at 90 by another set of trusses so that the verticals are common to both sets. Because of the rigid connections at the intersections, loads are distributed nearly equally to all trusses. Reduced truss depth and weight savings are among the apparent advantages of such grids.
Long-span joists are light trusses closely spaced to support floors and flat roofs. They conform to standard specifications (Table 7.1) and to standard loading. Both Pratt and Warren types are used, the shape of chords and webs varying with the fabricator. Yet, all joists with the same designation have the same guaranteed load supporting capacity. The standard loading tables list allowable loads for joists up to 72 in deep and with clear span up to 144 ft. The joists may have parallel or sloping chords or other configuration.
Truss Applications. Cross sections through a number of buildings having roof trusses of the general type just discussed are shown diagrammatically in Fig. 7.12. Cross section a might be that of a storage building or a light industrial building. A Fink truss provides a substantial roof slope. Roofs of this type are often designed
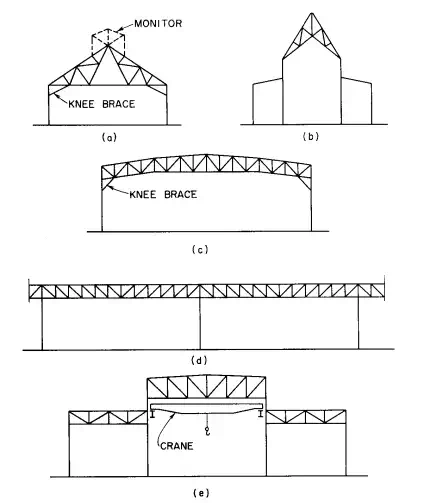
FIGURE 7.12 Some examples of structures with truss roofs
to carry little loading, if any, except that produced by wind and snow, since the contents of the building are supported on the ground floor. For light construction, the roof and exterior wall covering may consist of thin, cold-formed metal panels. Lighting and ventilation, in addition to that provided by windows in the vertical side walls, frequently are furnished by means of sash installed in the vertical side of a continuous monitor, framing for which is indicated by the dotted lines in the sketch.
Cross section b shows a scissors truss supporting the high roof over the nave of a church. This type of truss is used only when the roof pitch is steep, as in ecclesiastical architecture.
A modified Warren truss, shown in cross section c, might be one of the main supporting roof members over an auditorium, gymnasium, theatre, or other assembly-type building where large, unobstructed floor space is required. Similar trusses, including modified Pratt, are used in the roofs of large garages, terminal buildings, and airplane hangars, for spans ranging from about 80 up to 500 ft.
The Pratt truss (Fig. 7.12d) is frequently used in industrial buildings, while e depicts a type of framing often used where overhead traveling cranes handle heavy loads from one point on the ground to another.
Arches. When very large clear spans are needed, the bent framing required to support walls and roof may take the form of solid or open-web arches, of the kind shown in Fig. 7.13. A notable feature of bents a and b is the heavy steel pins at points A, B, and C, connecting the two halves of the arch together at the crown and supporting them at the foundation. These pines are designed to carry all the reaction from each half arch, and to function in shear and bearing much as a single bolt is assumed to perform when loaded in double shear.
Use of hinge pins offers two advantages in long-span frames of the type shown in Fig. 7.13. In the first place, they simplify design calculations. Second, they simplify erection. All the careful fitting can be done, and strong connections required to develop the needed strength at the ends of the arch can be made in the shop, instead of high above ground in the field. When these heavy members have been raised in the field about in their final position, the upper end of each arch is adjusted, upward or downward, by means of jacks near the free end of the arch. When the holes in the pin plates line up exactly, the crown pins is slipped in place and secured against falling out by the attachment of keeper plates. The arch is then ready to carry its loading. Bents of the type shown in Fig. 7.13a and b are referred to as three-hinged arches.
When ground conditions are favourable and foundations are properly designed, and if the loads to be carried are relatively light, as, for example, for a large gymnasium, a hinge less arch similar to the one shown diagrammatically in Fig. 7.13c may offer advantage in overall economy.
In many cases, the arches shown in Fig. 7.13a and b are designed without the pins at B (two-hinged arch). Then, the section at B must be capable of carrying the moment and shear present. Therefore, the section at B may be heavier than for the three-hinged arch, and erection will be more exacting for correct closure.
Rigid Frames. These are another type of long-span bent. In design, the stiffness afforded by beam-to-column connections is carefully evaluated and counted on in the design to relieve some of the bending moment that otherwise would be assumed as occurring with maximum intensity at midspan. Typical examples of rigid frame bents are shown in Fig. 7.14. When complete assembled in place in the field, the
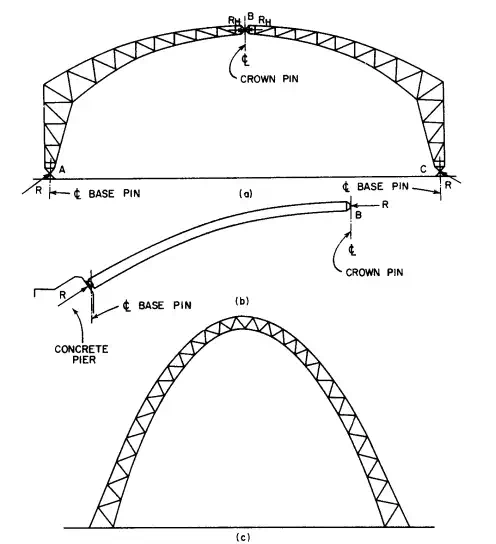
FIGURE 7.13 Steel arches: (a) and (b) three-hinged; (c) fixed.
frames are fully continuous throughout their entire length and height. A distinguishing characteristic of rigid frames is the absence of pins or hinges at the crown, or midspan.
In principle, single-span rigid-frame bents are either two-hinged or hinge less arches. For hinge less arches, the column bases are fully restrained by large rigid foundations, to which they are attached by a connection capable of transmitting moment as well as shear. Since such foundations may not be economical or even possible when soil conditions are not favourable, the usual practice is to consider the bents hinged at each reaction. However, this does not imply the necessity of expensive pin details; in most cases, sufficient rotation of the column base can be obtained with the ordinary flat-ended base detail and a single line of anchor bolts
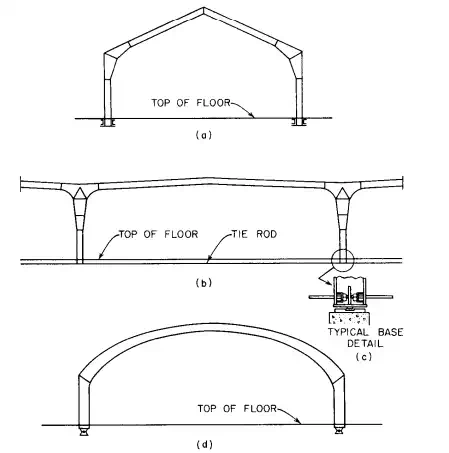
FIGURE 7.14 Steel rigid frames: (a) single bent; (b) continuous frame with underfloor tie; (c) connection of tie to a column; (d) with two-hinged.
placed perpendicular to the span on the column center line. Many designers prefer to obtain a hinge effect by concentrating the column load on a narrow bar, as shown in Fig. 7.14c; this refinement is worthwhile in larger spans.
Regardless of how the frame is hinged, there is a problem in resisting the horizontal shear that the rigid frame imparts to the foundation. For small spans and light thrusts, it may be feasible to depend on the foundation to resist lateral displacement. However, more positive performance and also reduction in costs are usually obtained by connecting opposite columns of a frame with tie rods, as illustrated in Fig. 7.14b, thus eliminating these horizontal forces from the foundation.
For ties on small spans, it may be possible to utilize the reinforcing bars in the floor slab or floor beams, by simply connecting them to the column bases. On larger spans, it is advisable to use tie rods and turnbuckles, the latter affording the opportunity to prestress the ties and thus compensate for elastic elongation of the rods when stressed. Prestressing the rod during erection to 50% of its value has been recommended for some major installations; but the foundations should be checked for resisting some portion of the thrust.
Single-story, welded rigid frames often are chosen where exposed steelwork is desired for such structures as churches, gymnasiums, auditoriums, bowling alleys, and shopping centres, because of attractive appearance and economy. Columns may be tapered, girders may vary in depth linearly or parabolically, haunches (knees) may be curved, field joints may be made inconspicuous, and stiffness may simply be plates.
Field Splices. One problem associated with long-span construction is that of locating field splices compatible with the maximum sizes of members that can be shipped and erected. Field splices in frames are generally located at or near the point of counter flexure, thus reducing the splicing material to a minimum. In general, the maximum height for shipping by truck is 8 ft, by rail 10 ft. Greater overall depths are possible, but these should always be checked with the carrier; they vary with clearances under bridges and through tunnels.
Individual shipping pieces must be stiff enough to be handled without buckling or other injury, light enough to be lifted by the raising equipment, and capable of erection without interference from other parts of the framework. This suggests a study of the entire frame to ensure orderly erection, and to make provisions for temporary bracing of the members, to prevent jackknifing, and for temporary guying of the frame, to obtain proper alignment.
Hung-Span Beams. In some large one-story buildings, an arrangement of cantilever-suspension (hung) spans (Fig. 7.15) has proved economical and highly efficient. This layout was made so as to obtain equal maximum moments, both negative and positive, for the condition of uniform load on all spans. A minimum of three spans is required; that is, a combination of two end spans (A) and one intermediate span (C). The connection at the end of the cantilever (point D) must be designed as a shear connection only. If the connection is capable of transmitting moment as well as shear, it will change the design to one of continuity and the dimensions in Fig. 7.15 will not apply. This scheme of cantilever and suspended spans is not necessarily limited to one-story buildings.
As a rule, interior columns are separate elements in each story. Therefore, horizontal forces on the building must be taken solely by the exterior columns.
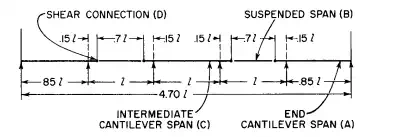
FIGURE 7.15 Hung- or suspended-span steel construction.
Comments are closed.