Floor screed is composed of cementitious materials and sand blended based on a suitable mix design and applied to provide a leveled surface for the floor finish which is introduced to the surface of the floor screed.
So, floor screed is the base for the floor finish and greatly influences the performance of floor finish. In this article, different aspects of floor screed will be explored.
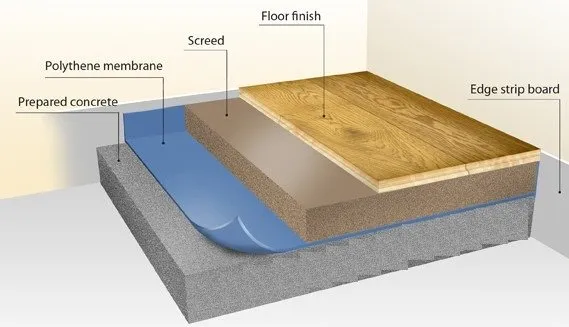
Fig.1: Details of Floor Screed
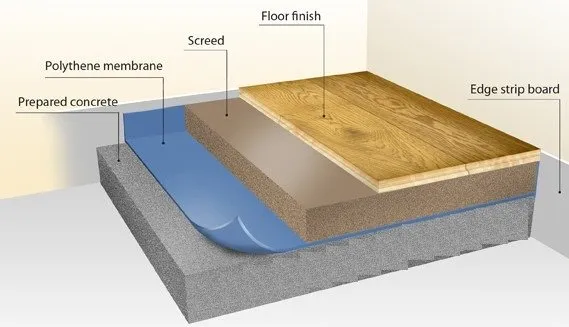
Fig.2: Floor Screed Construction
Following points regarding flooring screeds are discussed:
- Types of floor screed
- Floor screed materials
- What are the requirements that a floor screed should meet?
- Floor screeding procedure
- How a successful screed floor can be constructed?
Types of Floor Screed
There are different types of floor screed that is specified based on the requirements and applications and the functionality of the floor:
- Unbonded screed floor (Figure 3 and Figure 6)
- Bonded screed floor (Figure 3 and Figure 4)
- Floating screed floor (Figure 3 and Figure 5)
- Heated screed floor (Figure 3 and Figure 7)
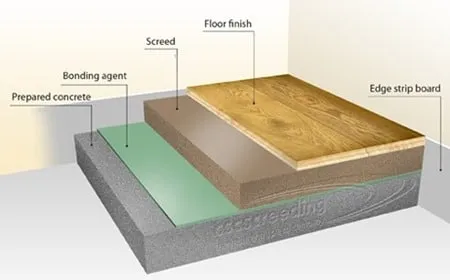
Fig.3: Different Types of Floor Screeds; (A) Bonded Screed, (B) Floated Screed, (C) Unbonded Screed and (D) Heated Screed

Fig.4: Bonded Screed Floor
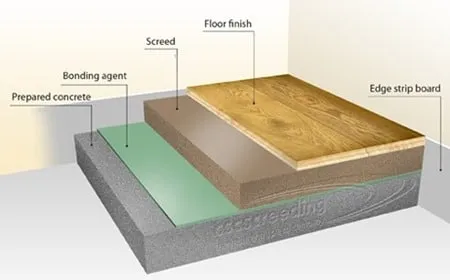
Fig.5: Floated Screed Floors

Fig.6: Unbonded Screed Floors
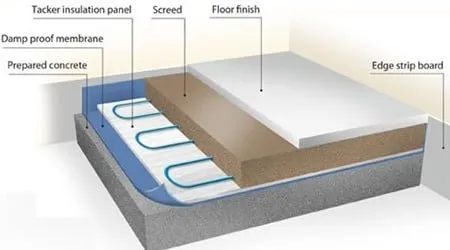
Fig.7: Heated Screed Floor
Materials for Floor Screed
Following are the materials used for construction of floor screeds:
- Cement
- Clean and sharp sand
- Water
- And occasionally additives are added to obtain specific properties. Polymer materials or metal mesh or glass are likely to be introduced to reinforce the screed.
The above components are adequately blended based on the prepared material proportions. If the thickness of the floor screed does not exceed 40mm, then the recommended mix is 1 Portland cement: 3 sands or 1 Portland cement: 4.5 sand.
However, 1 cement: 1.5fine sand: 3 coarse aggregate (10 mm maximum aggregate size) should be considered if the floor screed thickness is greater than 40mm.
It should be known that drying shrinkage gets reduced as the proportion of cement to sand is decreased.
Suitable amount of water should be specified to provide required workability since excessive water would reduce floor screed strength and inadequate water quantity lead to poor compaction.
What are the Requirements that a Floor Screed Should Meet?
Floor screeds should have adequate thickness which is based on the screed type and application frequencies. Recommended floor screed thickness based on the type of the screed floor and the construction conditions are provided in Table-1.
Table-1: Recommended Floor Screed Based on the Type of Screed and Construction Condition
Recommended floor screed thickness, mm | Floor screed type and construction condition |
12 | For monolithic construction. In this case floor screed will be placed no longer than 3 hours after the placement of concrete. This will guarantee a satisfactory bond between floor screed and placed concrete beneath it. |
40 | For screed floor placed on hardened concrete. The concrete should be cut by appropriate means then cleaned, wetted and finally screed is placed. Not only will this ensure good bond but also make the screed to dry slowly and prevent cracks. |
50 | For floor screed placed on impermeable damp proof membrane. In this case a bond between the screed and the layer below it would not exist and hence shrinkage is unrestrained. |
65 | For screed installed on compressible course of sound or heat insulation material. This is recommended for domestic application only, otherwise the thickness of the screed should be increased. Lesser thickness will suffer from crack development. |
75 | For screed installed on compressible course of sound or heat insulation material. This is advised for applications other than domestic utilization. Lesser thickness will suffer from crack development. |
- Floor screed strength should be 20MPa for domestic application and 30MPa for industrial utilization
- It should be solid and compact so as to provide satisfactory base for the floor finish
- It should be curried properly to prevent shrinkage and rapid drying which lead to cracks. So, it should undergo almost all shrinkage, which floor screed might experience, prior to applying floor finish. This will lead to prevent the initiation of cracks.
- Finally, floor screed surface should be flat and smooth.
Procedure of Floor Screeding
- Evaluate the surface of the base
- Estimate materials used for screeding
- Prepare the base
- Prepare the floor screed mixture
- Apply bonding agents such as water or bonding slurry
- Place the floor screed mixture
- Finally, properly cure the placed materials
How a Successful Screed Floor can be Constructed?
- Choose right and suitable screed contractor
- Select suitable screed floor type
- Produce right and suitable floor screed mixture
- Construct floor screed using appropriate and acceptable screed placement process
- Consider right approaches for floor screed protection