Iron and its alloys are generally referred to as ferrous metals. Even small amounts of alloy change the properties of ferrous metals significantly. Also, the properties can be changed considerably by changing the atomic structure of these metals by heating and cooling.
Types Of Irons And Steels
Steel is a solution of carbon in iron. Various types of steel are produced by varying the percentage of carbon added to molten iron and controlling the cooling, which affects the atomic structure of the product, and hence its properties. Some of the structural changes can be explained with the aid of an iron-carbon equilibrium diagram (Fig. 4.2).
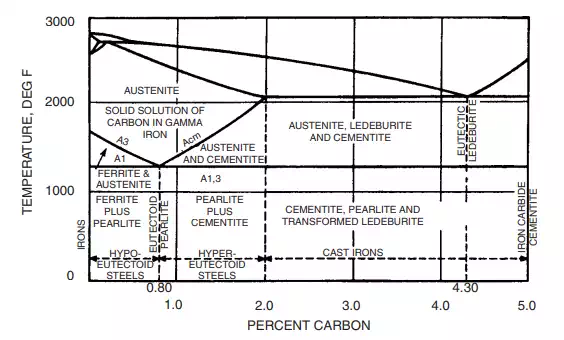
FIGURE 4.2 Iron-carbon diagram.
Iron-Carbon Equilibrium Diagram
The iron-carbon equilibrium diagram in Fig. 4.2 shows that, under equilibrium conditions (slow cooling) if not more than 2.0% carbon is present, a solid solution of carbon in gamma iron exists at elevated temperatures. This is called austenite. If the carbon content is less than 0.8%, cooling below the A3 temperature line causes transformation of some of the austenite to ferrite, which is substantially pure alpha iron (containing less than 0.01% carbon in solution). Still further cooling to below the A1 line causes the remaining austenite to transform to pearlite—the eutectoid mixture of fine plates, or lamellas, of ferrite and cementite (iron carbide) whose iridescent appearance under the microscope gives it its name.
If the carbon content is 0.8%, no transformation on cooling the austenite occurs until the A1 temperature is reached. At that point, all the austenite transforms to pearlite, with its typical ‘‘thumbprint’’ microstructure.
At carbon contents between 0.80 and 2.0%, cooling below the Acm temperature line causes iron carbide, or cementite, to form in the temperature range between Acm and A1,3. Below A1,3, the remaining austenite transforms to pearlite.
Types of Irons
Metals containing substantially no carbon (several hundredths of 1%) are called irons, of which wrought iron, electrolytic iron, and ‘‘ingot’’ iron are examples.
Wrought iron, whether made by the traditional puddling method or by mixing very low carbon iron and slag, contains a substantial amount of slag. Because it contains very little carbon, it is soft, ductile, and tough and, like low-carbon ferrous metals generally, is relatively resistant to corrosion. It is easily worked. When broken, it shows a fibrous fracture because of the slag inclusions. ‘‘Ingot’’ iron is a very low carbon iron containing no slag, which is also soft, ductile, and tough.
TABLE 4.16 ASTM Requirements for Structural, Reinforcing, and Fastening Steels*
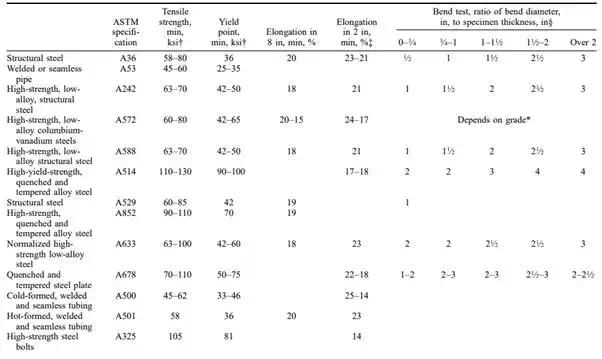
TABLE 4.16 ASTM Requirements for Structural, Reinforcing, and Fastening Steels* (Continued)
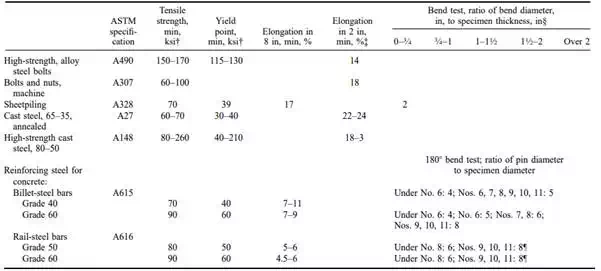
Above 2.0% carbon content is the region of the cast irons. Above the A1,3 temperature, austenite, the eutectic ledeburite and cementite occur; below the A1,3 temperature, the austenite transforms to pearlite, and a similar transformation of the ledeburite occurs.
When the silicon content is kept low, and the metal is cooled rapidly, white cast iron results. It is hard and brittle because of the high cementite content. White cast iron as such has little use; but when it is reheated and held a long time in the vicinity of the transformation temperature, then cooled slowly, the cementite decomposes to ferrite and nodular or temper carbon. The result is black-heart malleable iron. If the carbon is removed during malleableization, white-heart malleable iron results.
If the silicon content is raised, and the metal is cooled relatively slowly, gray cast iron results. It contains cementite, pearlite, ferrite, and some free carbon, which gives it its gray colour. Gray iron is considerably softer and tougher than white cast iron and is generally used for castings of all kinds. Often, it is alloyed with elements like nickel, chromium, copper, and molybdenum.
At 5.0% carbon, the end products are hard, brittle iron carbide or cementite.
Types of Carbon Steels
Most of the steel used for construction is low- to medium-carbon, relatively mild, tough, and strong, fairly easy to work by cutting, punching, riveting, and welding. Table 4.16 summarizes the most important carbon steels and low-alloy steels used in construction as specified by ASTM.
The plain iron-carbon metals with less than 0.8% carbon content consist of ferrite and pearlite and provide the low-carbon (0.06 to 0.30%), medium-carbon (0.30 to 0.50%), and high-carbon (0.50 to 0.80%) steels called hypo eutectoid steels. The higher-carbon or hypereutectoid tool steels contain 0.8 to 2.0% carbon and consist of pearlite and cementite. The eutectoid steels occurring in the vicinity of 0.8% carbon are essentially all pearlite.
The American Iron and Steel Institute and the Society of Automotive Engineers have designated standard compositions for various steels including plain carbon steels and alloy steels. AISI and SAE numbers and compositions for several representative hot-rolled carbon-steel bars are given in Table 4.17.
Prestressed concrete imposes special requirements for reinforcing steel. It must be of high strength with a high yield point and minimum creep in the working range. Table 4.16 and 4.18 give ASTM specification requirements for bars, wires, and strands. 4.40.4
Types of Structural Steels
Structural steels are low- to medium-carbon steels used in elements 1 ⁄4 in thick or more to form structural framing. The American Institute of Steel Construction (AISC) ‘‘Code of Standard Practice for Steel Buildings and Bridges’’ lists the elements that are included in the scope of the work in contract documents for structural steel. The list includes flexural members, columns, trusses, bearings and bearing plates, bracing, hangers, bolts and nuts, shear connectors, wedges, and shims. The AISC ‘‘Specification for Structural Steel Buildings’’ (ASD and LRFD) tabulates the types of structural steel that are approved for use in buildings. These steels are given in Table 4.16.
TABLE 4.17 Standard Steels for Hot-Rolled Bars
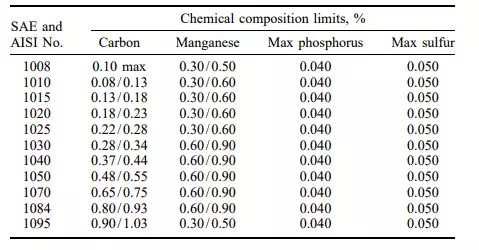
TABLE 4.18 ASTM Requirements for Prestressing Bars and Wires
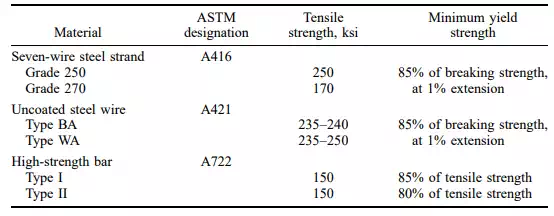
In accordance with present practice, the steels described in this section and in Sec. 7 are given the names of the corresponding ASTM specifications for the steels. For example, all steels conforming with ASTM A588, ‘‘Specification for High Strength Low-Alloy Structural Steel,’’ are called A588 steel. Further identification may be given by a grade, which usually indicates the steel yield strength.
Structural steels may be classified as carbon steels; high-strength, low-alloy steels; heat-treated, high-strength carbon steels; or heat-treated, constructional alloy steels.
Carbon steels satisfy all of the following requirements:
1. The maximum content specified for alloying elements does not exceed the following: manganese, 1.65%; silicon, 0.60%; copper, 0.60%.
2. The specified minimum for copper does not exceed 0.40%.
3. No minimum content is specified for other elements added to obtain a desired alloying effect.
A36 and A529 steels are included in this category.
High-strength, low-alloy steels have specified minimum yield strengths larger than 40 ksi, which are attained without heat treatment. A242, A572, and A588 steels are included in this category. A242 and A572 steel are often referred to as weathering steels, because they have higher resistance to corrosion than carbon steels. On exposure to ordinary atmospheric conditions, they develop a protective oxide surface.
Heat-treated, high-strength carbon steels are heat-treated to achieve specified high strength and toughness. A633, A678, and A852 steels are included in this category.
Heat-treated, constructional alloy steels contain alloying elements in excess of the limits for carbon steels and are heat-treated to obtain a combination of high strength and toughness. These are the strongest steels in general structural use. The various grades of A514 steel, with yield strengths up to 100 ksi, are in this category.