1.Submerged arc welding
• Weld arc is shielded by a granular flux , consisting of silica, lime,
manganese oxide,
calcium fluoride and other compounds.
• Flux is fed into the weld zone by gravity flow through nozzle
Thick layer of flux covers molten metal
• Flux acts as a thermal insulator ,promoting deep penetration of heat into the work piece
• Consumable electrode is a coil of bare round wire fed automatically through a tube
Power is supplied by 3-phase or 2-phase power lines
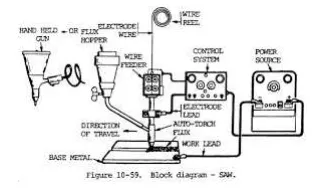
2.Laser Beam Welding (LBW)
Fusion welding process in which coalescence is achieved by energy of a highly concentrated, coherent light beam focused on joint
Laser = “light amplification by stimulated emission of radiation” LBW normally performed with shielding gases to prevent oxidation
Filler metal not usually added
High power density in small area, so LBW often used for small parts
Working
The laser WELDING system consists of a power source, a flash lamp filled with Xenon, lasing material, focusing lens mechanism and worktable. The flash tube flashes at a rate of thousands per second. As a result of multiple reflections, Beam power is built up to enormous level.
The output laser beam is highly directional and strong, coherent and unicromatic with a wavelength of 6934oA. It goes through a focusing device where it is pinpointed on the work piece, fusion takes place and the weld is accomplished due to concentrated heat produced. Laser beam welding process is shown in the figure.
Advantages.
1.Wide variety of metals can be welded. 2.Thermal damage is minimum.
3.Weld metal is purified.
4.Good ductility and mechanical properties. 5.Welds are vaccum tight.
6.filler metal is not used.
7.No effect on heat treated components.
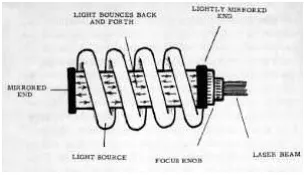
Limitations.
1.Low welding Speed.
2.Limited to thickness of 1.5mm. 3.Materials like Mg cannot be welded.
3.Electron Beam Welding (EBW)
Fusion welding process in which heat for welding is provided by a highly-focused, high-intensity stream of electrons striking work surface
Electron beam gun operates at:
High voltage (e.g., 10 to 150 kV typical) to accelerate electrons Beam currents are low (measured in milliamps)
Power in EBW not exceptional, but power density is
Working
The Kinetic energy of the electrons is converted into intense heat energy when the electrons are absorbed by the metal piece over a small area of the weld, producing deep penetration weld with a depth/width ratio as high as 15. This results in a narrow, almost parallel weld with very little distortion and a small width of the heat affected zone. There is no possibility of contamination by atmospheric gases because process is carried out in vaccum.
Advantages
High-quality welds, deep and narrow profiles
Limited heat affected zone, low thermal distortion High welding speeds
No flux or shielding gases needed
Disadvantages
High equipment cost
Precise joint preparation & alignment required Vacuum chamber required
Safety concern: EBW generates x-rays
Comparison: LBW vs. EBW
No vacuum chamber required for LBW No x-rays emitted in LBW
Laser beams can be focused and directed by optical lenses and mirrors
LBW not capable of the deep welds and high depth-to-width ratios of EBW
Maximum LBW depth = ~ 19 mm (3/4 in), whereas EBW depths = 50 mm (2 in)
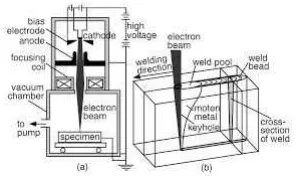
4.PLASMA ARC WELDING
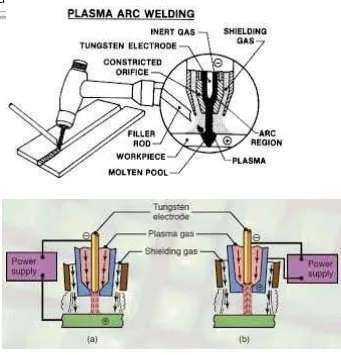
Principle:
Plasma Arc welding is a constricted arc process. The arc is constrained with the help of a water cooled small diameter nozzle which squeezes the arc, increases its pressure, temperature and heat intensely and thus improves stability, arc shape and heat transfer, characteristics
There are two methods of Plasma Arc Welding
(A) Transferred Arc
(B)Non- Transferred Arc.
(a)Transfered Arc
Here the electrical circuit is between the tungsten electode and the work piece. Work piece acts as anode and the tungsten electrode as cathode. The arc is transferred from the electrode to the work piece and hence the term transferred. Here the arc force is directed away from the plasma torch and into the work piece, hence capable of heating the work piece to a higher temperature.
(b)NON-Transferred Arc.
In Non-transferreed type, power is directly connected with the electrode and the torch of nozzle. The electrode carries the same current. Thus ,ionizing a high velocity gas that is strewing towards the workpiece. The main advantage of this type is that the spot moves inside the wall and heat the incoming gas and outer layer remains cool. This type of plasma has low thermal efficiency.
Advantages
1.Ensures arc stability. 2.Produces less thermal distortion
3.The process is readily automated.
Disadvantages.
1.Excessive noise is produced. 2.Equipment is complicated and expensive.
3.Large amount of ultraviolet and infrared rays are emitted.
5.THERMIT WELDING
FW process in which heat for coalescence is produced by superheated molten metal from the chemical reaction of thermite
Thermite = mixture of Al and Fe3O4 fine powders that produce an exothermic reaction when ignited
Also used for incendiary bombs
Filler metal obtained from liquid metal
Process used for joining, but has more in common with casting than welding
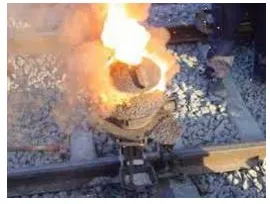
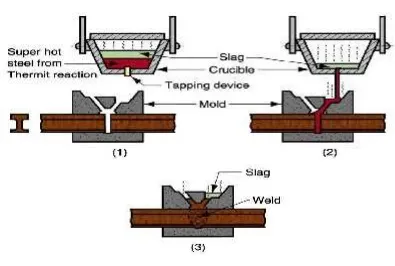
Fig: Thermit welding: (1) Thermit ignited; (2) crucible tapped, superheated metal flows into mold; (3) metal solidifies to produce weld joint.
Applications
joining of railroad rails
Repair of cracks in large steel castings and forgings
Weld surface is often smooth enough that no finishing is required
6.TIG& MIG WELDING
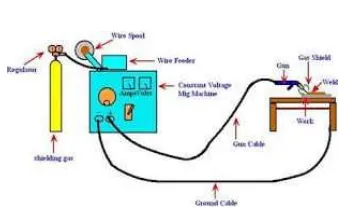
Inert Gas Welding
For materials such as Al or Ti which quickly form oxide layers, a method to place an inert atmosphere around the weld puddle had to be developed
Metal Inert Gas (MIG)
• Uses a consumable electrode (filler wire made of the base metal)
• Inert gas is typically Argon
Gas Tungsten Arc Welding (GTAW)
Uses a non-consumable tungsten electrode and an inert gas for arc shielding
Melting point of tungsten = 3410 C (6170 F) A.k.a. Tungsten Inert Gas (TIG) welding
In Europe, called “WIG welding” Used with or without a filler metal
When filler metal used, it is added to weld pool from separate rod or wire
Applications: aluminum and stainless steel most common
Advantages
High quality welds for suitable applications No spatter because no filler metal through arc
Little or no post-weld cleaning because no flux
Disadvantages
Generally slower and m ore costly than consumable electrode AW processes
7.RESISTANCE WELDING
Resistance Welding (RW)
A group of fusion weldin g processes that use a combination of heat and pressure to accomplish coalescence
Heat generated by electrical resistance to current flow at junction to be welded Principal RW process is res istance spot welding (RSW
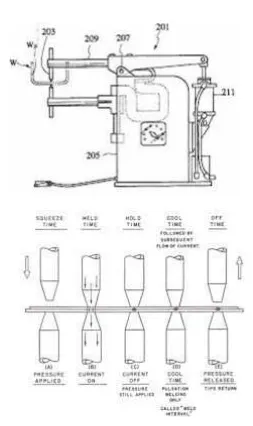
Components in Resistance Spot Welding
Parts to be welded (usually sheet metal) Two opposing electrod es
Means of applying pressure to squeeze parts between electrodes
Power supply from wh ich a controlled current can be applied for a specified time duration
Advantages
No filler metal required
High production rates p ossible
Lends itself to mechanization and automation Lower operator skill le vel than for arc welding
Good repeatability and reliability.
Comments are closed.