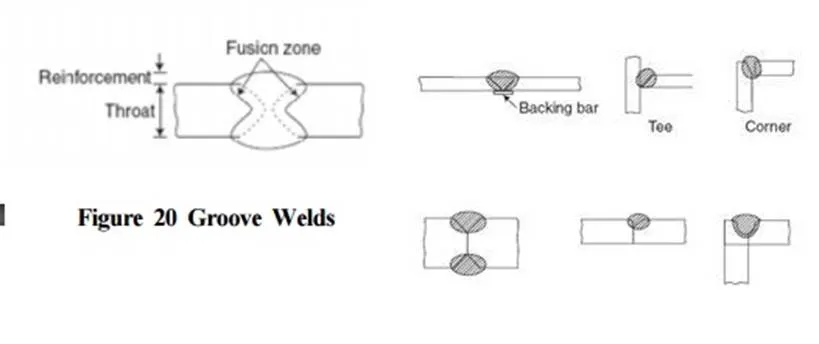
ASSUMPTIONS IN THE ANALYSIS OF WELDED JOINTS
The following assumptions are made in the analysis of welded joints.
� Welds connecting various parts are homogeneous, isotropic and elastic.
� The parts connected by welds are rigid and their deformations are therefore neglected.
� Only stresses due to external loads are to be considered. Effects of residual stresses, stress concentrations and shape of welds are neglected.
ANALYSIS AND DESIGN OF BUTT(GROOVE) WELDS
Groove welds are usually provided when the member is subjected to tension or compression. Since there is no change in the section at the joint, this is the most suitable form of joint to transfer alternating stress. However when the welds are intended to take shear stress, careful consideration should also be made so that the shear stresses developed is taken care of. Figure 20 shows the typical cross section of a groove weld. Square groove welds are usually employed for sections of thickness up to 8mm. If sections with more than 8mm thickness, U, V, double U or double V butt welds are used.
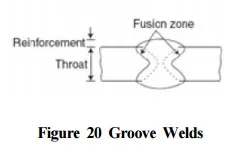
1. Reinforcement in Groove Welds
Extra weld material which is deposited to make the throat thickness at least 10% more than the welded material is known as reinforcement (see Figure 20). This will increase the efficiency of the joint. Reinforcement will increase the strength of grove welds under static loading. In the case of dynamic loading, reinforcement may result in stress concentrations. So the reinforcement is usually dressed flush in the case of members subjected to dynamic loading. However subsequent removal of reinforcement is not considered as reducing the strength of joint. The reinforcement is ignored in calculating the strength. In any case the reinforcement should not exceed 3mm.
2. Size of Groove Welds
Size of welded joint is usually specified by throat dimension. This is also called effective throat thickness. Groove welds may be classified in to full penetration groove welds (Figure 21) or partial penetration groove welds (Figure 22). Complete penetration is difficult to achieve in the case of single U, V, J and bevel welds. However, this can be achieved by using backing strips as shown in Figure 21.
As per Cl.10.5.3.3 of IS800-2007, the effective throat thickness of a complete penetration butt weld shall be taken as the thickness of the thinner part joined, and that of an incomplete penetration butt weld shall be taken as the minimum thickness of the weld metal common to the parts joined, excluding reinforcements. However in the case where full penetration groove welds cannot be achieved, an effective throat thickness of 1/8th of the thickness of thinner member is used. But for calculating the strength of the connection, a throat thickness of 5/6th of the thinner member is usually assumed.
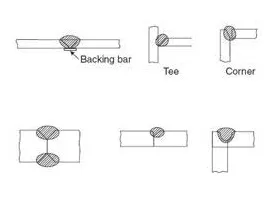
3. Effective area of Groove Welds
Effective area of weld is obtained as the product of effective length, ? of weld and effective thickness (throat thickness), ??of weld. As per Cl.10.5.4.2 of IS800-2007, the effective length of butt weld shall be taken as the length of the continuous full size butt weld, but not less than four times the size of the weld.
4. Design strength of Groove welds
Cl.10.5.7.1.2 of IS800-200 deals with the strength of Butt welds. As detailed in this clause of the code, Butt welds shall be treated as parent metal with a thickness equal to the throat thickness, and the stresses shall not exceed those permitted in the parent metal. Hence the following equations may be used for the design of butt welds.
The design strength of groove weld in tension and compression is given by Tdw=Tnw/rmw where Tnu is the nominal strength of the weld given by Tnw=fyLwtt and is partial safety factor of the material of the weld given by Table 5 of IS800-2007. Fy is the yield stress of the material, Lw is the effective length of the weld and Le is the throat thickness.
The design strength of groove weld in shear may be calculated by the expression Tdw=Tnw/rmw where ? is partial safety factor of the material of the weld given by Table 5 of IS800- ?is the nominal strength of the weld given by ? ? where ? is the 2007 and ? ????? ? ?. ultimate stress of the material, ?is the effective length of the weld and ? is the throat thickness.
5. Butt welds subjected to combination of stresses
Cl.10.5.10.2.2 deals with the case where fillet welds are subjected to combined bearing, bending and shear. Where bearing stress, fbr, is combined with bending (tensile or compressive), fb and shear stresses, q under the most in butt welds, the equivalent stress, fe, obtained from the formula fc = (fb2+fbr2+fbfbr+3q2)1/2. However the value of fe thus obtained shall not exceed the values allowed for the parent metal:
Comments are closed.